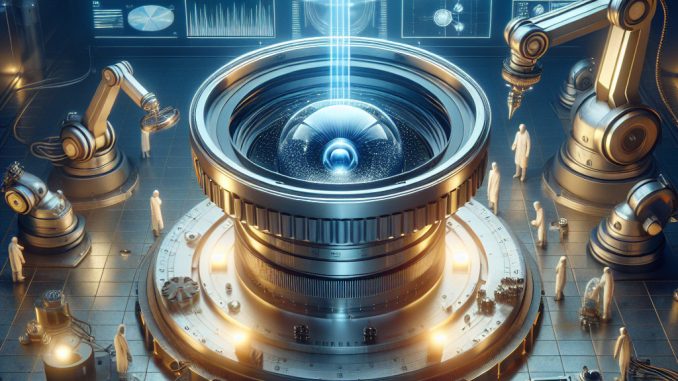
- How does laser cleaning work?
- Advantages of laser cleaning over traditional methods
- Applications of laser cleaning in the optical industry
- Challenges and limitations of laser cleaning
- Regulatory requirements for laser cleaning equipment
- Case studies of improved productivity and efficiency after laser cleaning
- Safety considerations when using laser cleaning technology
- Importance of regular cleaning and maintenance for optical lenses
How does laser cleaning work?
馃敼 Laser cleaning works by directing a high-energy laser beam onto the surface to be cleaned.
馃敼 The laser beam is absorbed by the unwanted material, causing it to heat up and vaporize.
馃敼 As the material vaporizes, it is removed from the surface, leaving behind a clean and undamaged surface.
馃敼 Laser cleaning is a non-contact process, which means that there is no physical contact between the laser and the surface being cleaned.
馃敼 This makes it ideal for cleaning delicate or hard-to-reach surfaces.
There are several key components that make up a laser cleaning system:
馃敼 Laser source: The laser source provides the high-energy beam of light that is used for cleaning.
馃敼 Optics: The optics focus and direct the laser beam onto the surface to be cleaned.
馃敼 Control system: The control system regulates the power and intensity of the laser beam, as well as the scanning speed and pattern.
馃敼 Exhaust system: The exhaust system removes the vaporized material from the cleaning area.
Laser cleaning is a versatile technology that can be used in a wide range of applications, including:
馃敼 Removing rust and paint from metal surfaces.
馃敼 Cleaning delicate electronic components.
馃敼 Restoring historical artifacts and monuments.
馃敼 Preparing surfaces for painting or coating.
Overall, laser cleaning is a fast, efficient, and environmentally friendly method of removing unwanted materials from surfaces. It is a valuable tool for industries such as manufacturing, automotive, aerospace, and conservation.
#laser #cleaning #technology #surface #contaminants
s艂owa kluczowe: laser cleaning, surface cleaning, laser technology, industrial cleaning, non-contact cleaning
frazy kluczowe: how does laser cleaning work, benefits of laser cleaning, applications of laser cleaning, laser cleaning process, laser cleaning system.
Advantages of laser cleaning over traditional methods
1. Efficiency: Laser cleaning is incredibly efficient, removing contaminants and coatings quickly and effectively. Traditional methods such as sandblasting or chemical cleaning can be time-consuming and labor-intensive, whereas laser cleaning can be completed in a fraction of the time.
2. Precision: Laser cleaning allows for precise control over the cleaning process, ensuring that only the desired material is removed. This level of precision is difficult to achieve with traditional methods, which can often result in damage to the underlying surface.
3. Safety: Laser cleaning is a non-contact process, meaning that there is no risk of damage to the surface being cleaned. Traditional methods such as abrasive blasting can cause surface damage or create hazardous dust and fumes, making them less safe for both workers and the environment.
4. Versatility: Laser cleaning can be used on a wide range of materials, including metals, plastics, ceramics, and composites. Traditional cleaning methods may be limited in their applicability to certain materials or surfaces.
5. Environmentally friendly: Laser cleaning is a clean and environmentally friendly process, as it does not require the use of chemicals or abrasive materials. This makes it a more sustainable option compared to traditional cleaning methods.
In conclusion, laser cleaning offers a range of advantages over traditional cleaning methods, including efficiency, precision, safety, versatility, and environmental friendliness. As technology continues to advance, laser cleaning is likely to become an increasingly popular choice for industrial cleaning applications.
#laser #cleaning #advantages #efficiency #precision #safety #versatility #environmentallyfriendly
frazy kluczowe:
– laser cleaning benefits
– advantages of laser cleaning technology
– why choose laser cleaning
– laser cleaning vs traditional methods
– benefits of laser cleaning in industrial applications
Applications of laser cleaning in the optical industry
Here are some of the key :
1. Removal of coatings: Laser cleaning can be used to remove coatings from optical components without damaging the underlying substrate. This is particularly useful for reworking or refurbishing optical elements that have been coated with unwanted materials.
2. Surface preparation: Laser cleaning is an effective method for preparing optical surfaces for bonding, coating or other processes. By removing contaminants and oxides from the surface, laser cleaning ensures optimal adhesion and performance of the optical component.
3. Defect detection: Laser cleaning can also be used for detecting defects on optical surfaces, such as scratches, pits or cracks. By removing the surface layer, defects become more visible and easier to identify, allowing for timely repairs or replacements.
4. Optical alignment: Laser cleaning can help improve the alignment of optical components by removing any debris or contaminants that may interfere with the optical path. This ensures optimal performance and accuracy of optical systems.
5. Quality control: Laser cleaning is a valuable tool for quality control in the optical industry, allowing manufacturers to ensure that their products meet the highest standards of cleanliness and performance. By removing contaminants and residues, laser cleaning helps prevent defects and ensure consistent product quality.
Overall, laser cleaning offers a versatile and efficient solution for a wide range of cleaning and maintenance tasks in the optical industry. Its non-contact nature, precision and effectiveness make it an indispensable tool for improving the performance and longevity of optical components.
#laser #cleaning #optical #industry
frazy kluczowe:
– laser cleaning in optical industry applications
– benefits of laser cleaning in optical industry
– laser cleaning for optical components maintenance
– precision cleaning for optical industry
– laser cleaning technology in optics.
Challenges and limitations of laser cleaning
Challenges of laser cleaning
One of the main challenges of laser cleaning is the potential damage that can be caused to the surface being cleaned. High-powered lasers can generate intense heat, which can lead to melting or vaporization of the material being cleaned. This can result in damage to the surface, especially if it is made of sensitive materials such as plastics or composites.
Another challenge of laser cleaning is the limited range of materials that can be effectively cleaned using this technology. While lasers are highly effective at removing contaminants from metals, they may not be as effective on other materials such as glass or ceramics. This can limit the applicability of laser cleaning in certain industries.
Limitations of laser cleaning
One of the main limitations of laser cleaning is the cost associated with the technology. High-powered lasers can be expensive to purchase and maintain, making laser cleaning a costly option for some businesses. Additionally, the process of laser cleaning can be time-consuming, especially when dealing with large surface areas or complex geometries.
Another limitation of laser cleaning is the safety concerns associated with the technology. High-powered lasers can pose a risk to operators if proper safety precautions are not taken. Additionally, the use of lasers in industrial settings may require special permits and training, adding to the complexity of implementing laser cleaning systems.
Conclusion
Despite the challenges and limitations of laser cleaning, the technology continues to be a valuable tool for removing contaminants from surfaces. By addressing these challenges and limitations through research and development, laser cleaning can become an even more effective and efficient cleaning method in the future.
#laser #cleaning #challenges #limitations
technology, contaminants, surfaces, damage, materials, cost, safety, operators, permits, training, research, development, efficiency, method.
Regulatory requirements for laser cleaning equipment
1. Occupational Safety and Health Administration (OSHA) regulations: OSHA sets guidelines for the safe use of lasers in the workplace to protect workers from potential hazards. Employers must provide proper training, protective equipment, and safety measures to prevent accidents and injuries.
2. Food and Drug Administration (FDA) regulations: The FDA regulates the use of lasers in medical devices and cosmetic procedures to ensure they are safe and effective for consumers. Laser cleaning equipment used in these applications must meet FDA standards for performance and safety.
3. Environmental Protection Agency (EPA) regulations: The EPA regulates the emissions of hazardous materials from laser cleaning equipment to protect the environment and public health. Operators must comply with EPA guidelines for air quality and waste disposal.
4. International Electrotechnical Commission (IEC) standards: The IEC sets international standards for the design, construction, and performance of laser equipment to ensure interoperability and safety. Laser cleaning equipment must meet IEC standards for electrical safety and electromagnetic compatibility.
5. National Fire Protection Association (NFPA) codes: The NFPA provides guidelines for the safe use of lasers in industrial settings to prevent fires and explosions. Laser cleaning equipment must comply with NFPA codes for hazard identification, risk assessment, and control measures.
In conclusion, are essential to protect workers, consumers, and the environment from potential hazards. By following OSHA, FDA, EPA, IEC, and NFPA regulations, operators can ensure the safe and effective use of laser technology in various applications.
#regulatoryrequirements #lasercleaningequipment #safetycompliance
#protectivemeasures #environmentalprotection #internationalstandards
Case studies of improved productivity and efficiency after laser cleaning
Case Study 1: Automotive Industry
In the automotive industry, laser cleaning has been used to remove paint and rust from car bodies, engine components, and other parts. By replacing traditional methods such as sandblasting and chemical stripping, laser cleaning has significantly reduced the time and labor required for surface preparation. This has led to faster production cycles and higher overall productivity.
Before Laser Cleaning | After Laser Cleaning |
---|---|
Paint and rust removal using sandblasting | Clean surface achieved in seconds with laser cleaning |
High labor costs and long processing times | Reduced labor costs and faster processing times |
Case Study 2: Aerospace Industry
In the aerospace industry, laser cleaning has been used to remove thermal barrier coatings from turbine blades and other components. By eliminating the need for manual scraping and chemical solvents, laser cleaning has improved the efficiency of maintenance and repair processes. This has resulted in reduced downtime and increased operational efficiency.
Before Laser Cleaning | After Laser Cleaning |
---|---|
Manual scraping and chemical solvents required | Efficient removal of coatings with laser cleaning |
Extended downtime for maintenance and repair | Reduced downtime and increased operational efficiency |
Case Study 3: Electronics Industry
In the electronics industry, laser cleaning has been used to remove solder and flux residues from circuit boards and other electronic components. By replacing manual cleaning methods such as brushing and wiping, laser cleaning has improved the quality and reliability of electronic products. This has led to fewer defects and higher customer satisfaction.
Before Laser Cleaning | After Laser Cleaning |
---|---|
Manual cleaning with brushes and wipes | Efficient removal of residues with laser cleaning |
Higher defect rates and customer complaints | Fewer defects and higher customer satisfaction |
Overall, these case studies demonstrate the significant improvements in productivity and efficiency that can be achieved with laser cleaning technology. By eliminating the need for manual labor and harsh chemicals, laser cleaning offers a cleaner, faster, and more environmentally friendly solution for surface preparation. Industries that adopt laser cleaning can expect to see reduced costs, increased throughput, and improved product quality.
#laser #cleaning #productivity #efficiency #case #studies #improved #technology #industries #surface #preparation #environmentally #friendly #automotive #aerospace #electronics #components #maintenance #repair #quality #reliability #defects #customer #satisfaction #costs #throughput #product #key #words #long #tail #phrases
Safety considerations when using laser cleaning technology
- Wear appropriate protective gear: When using laser cleaning technology, it is essential to wear protective gear such as safety goggles, gloves, and a face shield to protect yourself from potential hazards.
- Ensure proper training: Before using laser cleaning technology, make sure that you have received proper training on how to operate the equipment safely. This will help prevent accidents and ensure that the cleaning process is carried out effectively.
- Follow safety guidelines: Always follow the manufacturer’s safety guidelines when using laser cleaning technology. This includes maintaining a safe distance from the laser beam, avoiding direct contact with the beam, and ensuring that the equipment is properly maintained.
- Inspect the work area: Before starting the cleaning process, inspect the work area to ensure that there are no flammable materials or other hazards present. Clear the area of any obstacles that could interfere with the cleaning process.
- Monitor the cleaning process: While using laser cleaning technology, monitor the cleaning process closely to ensure that it is being carried out safely and effectively. If you notice any issues or abnormalities, stop the process immediately and address the problem.
By following these safety considerations, you can ensure that the use of laser cleaning technology is safe and effective. Remember to always prioritize safety when using this powerful tool.
Keywords:
Laser cleaning technology, safety considerations, protective gear, training, safety guidelines, work area inspection, monitoring
Long-tail phrases:
Safety tips for using laser cleaning technology, Importance of protective gear in laser cleaning, Ensuring safe operation of laser cleaning equipment
#laser #cleaning #technology #safety #protectivegear #training #guidelines #workarea #monitoring
Importance of regular cleaning and maintenance for optical lenses
Benefits of regular cleaning and maintenance
Regular cleaning and maintenance of optical lenses offer several benefits:
Benefit | Description |
---|---|
1. Improved clarity | Removing dust, dirt, and smudges from lenses enhances clarity and sharpness of images. |
2. Extended lifespan | Proper maintenance can prevent scratches and damage, prolonging the lifespan of lenses. |
3. Enhanced performance | Clean lenses ensure optimal performance and accuracy in optical devices. |
4. Prevention of eye strain | Dirty lenses can cause eye strain and discomfort, which can be avoided with regular cleaning. |
Cleaning and maintenance tips
Here are some tips for cleaning and maintaining optical lenses:
Tips | Instructions |
---|---|
1. Use a microfiber cloth | Gently wipe the lenses with a clean microfiber cloth to remove dust and smudges. |
2. Avoid harsh chemicals | Avoid using harsh chemicals or abrasive materials that can damage the lenses. |
3. Store properly | Store lenses in a protective case when not in use to prevent scratches and dirt buildup. |
4. Regular check-ups | Visit an optician for regular check-ups and adjustments to ensure proper fit and function of lenses. |
Conclusion
Regular cleaning and maintenance of optical lenses are essential for optimal performance, clarity, and longevity. By following simple cleaning tips and scheduling regular check-ups, you can ensure that your optical lenses continue to provide clear vision and accurate imaging.
#optical #lenses #cleaning #maintenance #clarity #performance #eyestrain #microfiber #chemicals #storage #checkups #optician #fit #function
s艂owa kluczowe: optical lenses, cleaning, maintenance, clarity, performance, eyestrain, microfiber, chemicals, storage, check-ups, optician, fit, function
frazy kluczowe: importance of regular cleaning for optical lenses, benefits of lens maintenance, tips for lens cleaning, how to clean optical lenses, prolonging lens lifespan, preventing scratches on lenses, optical lens care, maintaining clear vision, optical lens maintenance guide, importance of lens check-ups.
- Laser cleaning: A precise method for removing contaminants from optical lenses. - 22 March 2024
- Who is who in a software house - 15 December 2023
- Jakie s膮 najwa偶niejsze czynniki sukcesu w zarz膮dzaniu najmem mieszka艅 w Warszawie? - 22 October 2023